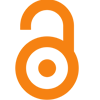
Review Article
Volume-1 Issue-1, 2021
Suitable Train of Bioremediation Techniques for Secondary Treatment of Drill Cuttings
Received Date: September 13, 2021
Accepted Date: October 13, 2021
Published Date: October 14, 2021
Journal Information
Switch to Full Text Menu
Abstract
Oil and gas exploration produces an overwhelming volume of wastes known for polluting the environment with immense negative impacts. One of such wastes is the drill cuttings incorporated with hazardous hydrocarbons, heavy metals and chemical additives from muds. Like other petroleum industry wastes, drill cuttings negatively affects the physical environment, alters the healthy chemical composition of the environment and exhibits toxic effects on sensitive organisms including humans. To offset these negative impacts variety of treatment options are available. Common physicochemical methods used for mitigating drill cuttings and their effects are thermal desorption, microwave heating, incineration, and solidification and stabilization. These options generate secondary contamination unlike the biological option, limited by land farming, composting and biopiling. Amongst these three options, the land farming method is most popular because it serves both treatment and disposal option and is compatible with the other two. Pretreatment of drill cuttings in composting and biopiling yield ten times efficiency in comparison to land farming treatment alone. This paper therefore suggests that drill cuttings be pretreated through composting and biopiling before the land farming option in order to reduce the overall treatment time.
Key words
Hermetia Illucens; Glutathione Antioxidant; Oxidative Stress; Malathion
Glutathione antioxidant system |
Developmental stage |
r |
Equation |
Type of equation |
R2 |
GPx |
5th larval instar |
0.54* |
Y= 244X |
Linear |
0.33 |
Adult |
0.24 |
Y= 656X |
-0.71 |
||
GR |
5th larval instar |
0.41 |
Y=1502X |
-0.25 |
|
Adult |
0.87** |
Y=1521X |
-0.53 |
||
G-S-T |
5th larval instar |
0.48 |
Y=2774X |
-2.35 |
|
Adult |
-0.44 |
Y=2798X |
-29.7 |
![]() |
Figure 1: A schematic diagram of drill cuttings formation and management options (Huang et al., 2018) |
![]() |
Figure 2: Hierarchy order of waste prevention suitable for drill cuttings management [38] |
Introduction
Drill cuttings are byproducts of oil and gas exploration activities and consist of hydrocarbons, heavy metals, salts and additives of drilling muds. Drilling wastes, including drill cuttings, ranked second to produced water, which is the highest source of oil and gas industry wastes [1]. Drill cuttings are from two sources: water-based muds (WBMs) and non-aqueous drilling fluids (NADFs). The latter comprises of oil-based muds (OBMs) and synthetic-based muds (SBMs) that are less friendly to the environment but generate lesser amount of drill cuttings [2]. This implies that drill cuttings emanating from OBMs and SBMs are more toxic to the environment and less susceptible to degradation in comparison to WBMs. The constituents of drill cuttings, including polyaromatic hydrocarbons, heavy metals and chlorides affect the environment and its receptors negatively through alteration of the physical features of the affected area [3, 4], offsetting of healthy chemical integrity of the environment resulting in compromised support for sensitive organisms [5], and distortion of innate microbial diversity and food chain [6, 7]. In addition, drill cuttings are phytotoxic, cytotoxic and genotoxic [8, 9].
In order to reduce or correct these defects, different remediation techniques are often put in place. These techniques can either be physical, chemical or biological. The management of drill cuttings borders on waste minimization, secondary treatment, biological treatment and disposal [10]. Most common secondary treatments used in managing drill cuttings are microwave heating, thermal desorption, incineration, and solidification and stabilization [11, 12, 13]. Some of these treatment/management technique serves as an alternative option but hardly can anyone of them be seen as sustainable since they can all lead to secondary pollution [14]. Waste treatment techniques that possess green and sustainable value are those of biological. Bioremediation techniques meant to address environmental pollution are numerous but only few have been used to mitigate drill cuttings. These techniques are land farming, composting and biopiling. However, land farming is more popular because it can both serve as treatment and disposal option. Land farming has both its merits and demerits but how its performance index can be improved is a concern to professionals in field.
Thus, this mini review probes into existing body of literature in finding out measures or approaches that can improve the performance of the land farming option for the management of drill cuttings. It is shown in this paper that sequential treatment of drill cuttings through composting, biopiling and land farming improves the treatment performance by a factor ten in comparison to using land farming alone. Alongside, the treatment process of land farming was highlighted and conditions that will enhance performance of the land farming was mentioned.
Definition of drill cuttings
Drill cuttings are crushed rock particles produced as the rotary drill bit penetrates into rock earth. The cuttings are transported, as lubricant, to the surface through the drilling (fluid) mud [15]. Meaning drill waste is made up of cuttings (consisting of metal oxides and heavy metals), and residual drilling mud [16]. Most dominant oxides found in dry drill cuttings are silicon (iv) oxide (SiO2), aluminum oxide (Al2O3) and barium oxide (BaO) while the dominant heavy metals are sinc (Zn), chromium (Cr), nickel (Ni), arsenic (As), copper (Cu) and lead (Pb) [17]. It is noteworthy that the chemical composition of drill cuttings rely on the rock types and the drill mud used [18, 1] itemized wastes associated with drilling: spent oil-based muds (mineral oil and whole mud, as major components), oil-based muds cutting (formation solids, oil-based muds as major components) and spent water-based muds (biodegradable matters, mineral oil and whole muds, as major components). Core drilling methods does not produce cuttings; rather they produce rock solid cylinders [19].
Classification/functions of drilling muds
There are two common categories of drilling muds: water-based muds and non-aqueous drilling fluids- WBMs and NADFs. The former consist of water (fresh or salty), barite (BaSO4; as weighting agent), clay or organic polymer, inorganic salts, inert solids and organic additives (physical property modifications). The NADFs are of two types: oil-based muds (OBMs) and synthetic-based muds (SBMs) [20]. The OBMs and SBMs are preferred over the WBMs on many aspects including cleaner hole drilling, generation of lesser drill cutting wastes, minimal drilling problems and suitability on high temperature/pressure well and horizontal wells [21]. However, on the ground of environmental impact, the WBMs are preferred over the non-aqueous drilling fluids. Field study has shown that WBMs are used where drilling would not go beyond one hundred metre [22]. Again, between the OBMs and SBMs, the SBMs have lesser toxicity, more susceptible to microbial degradation, recyclable and potential for bioaccumulation is lower [10].
Drilling is necessary for oil exploration during which drilling fluids (also called muds) are constantly pumped down the well, lubricate and cool the drill bit, stabilize the well bore and control the downhole pressure [23]. The purpose of the pressure control is to avoid blow-out and it is achieved through fluid density control which balances the downhole pressure [10]. The drill mud also transport the cuttings to the surface, where separation between the mud and cuttings occur through mechanical shaker (Figure 1). The mud are recycled until its usefulness becomes expired and unsuitable for the drilling operations. It is usually difficult to completely separate the mud from the drilled solids [24]. Thus, drill cuttings are a mixture of soil material, formation particles, base mud and in some cases reservoir fluids. The associated hydrocarbon of drill cuttings is called “oil on cutting” (OOC) or “base fluid retained on cuttings” BFROC [25].
Their Impacts in The Environment
The presence of rare earth metals heavy metals (their oxides and salts), including PAHs and chemical additives, in spent drill waste make it a potential source of toxicity [16]. However, the possible impact depends on the subterranean material, concentration, biotic community and length of exposure of biotic community. Overall, the ecological impact of drill cuttings wastes is appreciated after chronic exposure (three months at least) of biotic community since concentration of cutting waste are comparatively low (Bevandic et al., 2021). Several researchers have studied the impact of these wastes. Hazardous properties of discharged drill cuttings are shown through:
1. Changes in the physical features and chemical composition of the seafloor sediments when drill cuttings are discharged into the sea, including heavy metal pollution [3]. The persistency of the drill cuttings depends on the bottom water energy, reactivity of incorporated compounds and biodegradability [4]
2. Reduced light penetration caused by drill cuttings decreases the number of phytoplankton in the water column [26]
3. Reduction of soil oxygen contents due to decreased oxygen diffusion, ultimately leading to pseudo anaerobic condition [5]
4. Inhibits redox enzymatic processes, which reduces the fertility and biological activity of soil; and formation of water soluble humates due to drill cuttings alkaline reaction [9]
5. High salt-content drill cuttings creates water stress, causing plants wilt and death (McFarland, 2017)
6. Physical clogging of particles (from the drill cuttings) to zooplankton digestive tract and gills but crustaceans and fishes avoid drill cuttings suspended plumes [27].
Consequently, safety regulations are put in place for drill wastes management and disposals.
Management of Drilling Wastes
Drilling waste (including drill cuttings) is second to produced water, which is the largest volume of wastes generated in the oil and gas exploration and production industry [31]. Diverse means and methods are in operation to manage these drilling wastes with two objectives in mind: avoidance of undue delay of drilling operations and compliance with regulations imposed by governments and relevant institutions [32]. As a principle, waste management are required to follow a hierarchy order (Figure 2) of waste prevention, reuse, recycle and dispose [33]. Amongst the various available technologies and techniques, no particular option is preferable in all scenario because management options are determined by basic factors. These factors include regulations, type of base fluid used, transport and infrastructure among others [34]. Further, there are factors, which are specific for a chosen option, including reliability, performance, cost and portability [27]. The effect of the consideration of these factors is to ensure that best available management options are used.
There two phases of drilling waste management, which are solid control phase and secondary treatment phase. The solid control phase is concerned with the management of the quantity and quality of the generated waste volume [7]. The treatment phase is concerned with meeting criteria of disposal of the solid produced in the first phase. These two phases ate interlinked and cannot be operated in isolation. This is because the performance of the solid control phase conditions the type of secondary treatment that would be used and the secondary treatment technique in use would predispose the type of fluid selection, which in turn would determine the solid control technique. The goal of the solid control system is to reduce well cost by fast, efficient drill particles removal and minimization of liquid loss [35]. The process of the solid control system uses different pieces of equipment arranged in series starting with the shale shaker, powered by mechanical energy [36]. Though the shale shaker separates the cuttings from the drilling fluids and waste minimization, the recovered drilling mud may be processed using centrifuges or hydrocyclones to remove the finer particles that escaped the shale shaker [37].
The secondary treatment technology aims at reducing the residual amount of drilling muds attached to the cutting, which invariably increase the recoverable drilling fluids and ultimately saving cost. From environmental point of view, the final wastes contain lesser concentration with lesser environmental impact. Methods used for this purpose are physical, chemical and biological. In most cases, oil-based fluids are followed with secondary treatment because they tend to be far more hazardous [39]. Table 1 summarises the physical and chemical methods used for the secondary treatment. Some of these secondary treatment is followed by disposal, including but not exclusive to:
1. Offshore discharge. This is done once relevant discharge criteria are met. 2. Pit burial option. This option requires disposal of segregated cutting in an on-site pit earlier used for storing spent drilling fluids and cuttings. However, the liquid portion of the spent drilling fluid must have completely evaporated [10]. The liquid component of the drilling wastes is open to three options: being dislodge to surface water, land spreading or subsurface injection. One major disadvantage of this approach is that safe groundwater aquifer is contaminated. 3. Landfill option. It is meant to dispose inert wastes from oil and gas exploration. It has a bottom and top (used during non-active periods) liners to avoid groundwater contamination and evaporation respectively. The top liner is installed permanently when the landfill has served its purpose [40] 4. Re-injection option. Drill cuttings are injected into subsurface formation in the form of slurries using waste and water. 5. Solidification/stabilization (S/S) process. This method uses pozzolanic materials including cement and fly ash such that the physicochemical and handling properties of the wastes are improved alongside with the mitigation of the wastes’ toxicity, mobility and solubility [41]. 6. Incineration technique. Involves the controlled heating the material to a temperature of 820 to 1600 to inert residue (Nemerow, 2007). Waste material incinerators have been limited to rotary kiln and liquid injection. In the rotary kiln handles enormous solid and liquid wastes while the liquid injection requires feeding of liquid waste along with fuel in the presence of air [42]. 7. Thermal desorption process. Unlike incineration method, thermal desorption operate at 600 to volatilize water and hydrocarbons for off-gas treatment: particulate removal, condensation-carbon desorption, gas condensation-separation for heavier hydrocarbon separation [43] 8. Microwave heating method. In this method energy is directly but selectively transferred to materials through molecular interaction with the generated electromagnetic field unlike in heating operation where energy is transferred via conduction, convection and radiation [13].
These physical methods no matter how effective they might be lack sustainability factor which is the in-thing science of today. For this purpose, different variants of bioremediation options have been put in place to treat drill cuttings and other waste materials alike.
Suitable Bioremediation Techniques for Drill Cuttings
Bioremediation is any process that makes use of organisms, their parts or their enzymes to detoxify and restore contaminated environmental media to its former safe condition (Juwarka et al., 2014). As a biotechnology approach, bioremediation may be employed to decontaminate specific contaminants organic matter including drill cuttings [44]. Though multiple variants of bioremediation techniques exist for the treatment of oil wastes, only few are available for drill cuttings management. They include land farming (land treatment, land spreading), biopiles and composting [45, 46]. stated that land farming and composting are the two bioremediation methods employed by the Kuwat Institute for Scientific Research. Land farming is a type of land application among others. Land application refers to the deliberate incorporation of drill cutting to top soil in a controlled manner with the objective of allowing biotic factors interact and transform, metabolize and assimilate components of the wastes [47]. It has different terminologies:
• Land farming, which is concerned with the repeated application of the wastes on surface soil • Land spreading, which is one-off spreading of the wastes on shallow subsoil. • Land-spray while drilling (LWD) involves the spraying of drilling wastes from water-based drilling muds onto the soil surface [48] • Mix-bury-cover has to do with the mixing of the drilling wastes with subsoil, forming a stabilized mass that stays below the rooting zones (McFarlan et al., 2009). • Pump-off treatment refers to the pumping of the liquid portion of the wastes onto the land using simple irrigation tools (Duric, 2012)
This treatment technique is simple, cost effective and sustainable but constrained by regulatory requirements. This is because the land application feasibility varies with respect to the regulatory structure and country requirements [49]. Amongst these land application varieties, land farming is the most popular thus require a considerate elaboration. The treatment of oily wastes in the petroleum industry using land farming started when it became established that microorganisms can assimilate hydrocarbons [50, 51].
Land farming
Land farming has been used in the oil and gas exploration industries for a considerable number of years. It involves the repeated and controlled application of (oil) wastes to the surface soil allowing the autochthonous microorganisms to transform the hydrocarbons, metals and other waste components. In most cases, the adapted microorganisms utilizes the organic components of the wastes as their sole source of carbon and energy or fortuitously degrade hydrocarbons that they cannot use as carbon source. Apart from being a cost-friendly spent drill cuttings management method, land farming dilute metal and hydrocarbon concentration, reduces fertilizer losses, improves the water-retaining capacity of sandy soil and improves phytostabilization of soil [52, 53, 54]. Soil amendment (with calculated nutrients, water and organic manure) and regular tilling of the surface soil in question, improves performance optimization [55]. Besides, soil amendment, watering and tilling reduces leaching conditions, minimize inorganic compounds mobilization, maintains moisture control, increase aeration and reduce dust formation [56]. Land farming process require consistent monitoring of wastes attenuation and biodegradation including control mechanism to avoid conditions that will lead to runoff.
Basic approach in land farming treatment process for drill cuttings is straightforward and simple, and takes the following steps:
• Drill cuttings is transited from well site(s) using trucks and placed in a dedicated pit • Removing pastures, topsoil and leveling of the land in sequence • Drill cuttings is amended with sawdust for waste stabilization and waste concentration reduction • Pre-amended waste is transported by truck and excavator to the prepared land and spread on the land surface (reason for the name: land spreading) using a bulldozer • Removed topsoil is replaced in addition with organic manure for stability and nutrient enrichment. In addition, earthworms can be applied for aeration and nutrient enhancement • Required layer (less than six inches) of the ready treatment bed is established using a disc or a tractor • The treatment bed is levelled using harrows or chains • Timed tilling, watering (reason for the name: land farming) and monitoring is carried out routinely. Monitoring may require liners and monitoring wells • After a reduction of TPHs, heavy metals and salts to a regulatory benchmark, special plant species can be cultivated for further attenuation of wastes through phytoremediation • Next treatment phase should commence three years after decommissioning
It is however important to know that the choice to apply land farming rests on the drilling wastes’ chemical composition and the characteristics of the land to be used. Thus, physicochemical analyses the native soil and chemical analysis of the drill cuttings should be the first step to take in the remediation of drill cuttings using land farming [57]. Some of the key analyses to be conducted include but not limited to soil texture, total heavy metals, total salts (electrical conductivity), sodium adsorption ratio (SAR), total petroleum hydrocarbons (TPHs), routine soil nutrient analyses, extractable individual ions and cation exchange capacity. [58] noted that texture, hydraulic conductivity, bulk density, cation exchange capacity and nutrient status are soil properties that influences the extent and rate of hydrocarbon elimination. The results from these analyses can tell if the proposed land can be used for the remediation purpose. For instance land with chloride greater than 500 ppm, groundwater less than ten feet and inorganic compound pollution history will not be suitable for land farming remediation of drill cuttings [59]. The TPHs, heavy metals and salt concentrations are the most critical parameters to look out for from the drill cuttings. It is expected that the mixture of the drill cuttings and the top soil of the land in question should yield less than 1% TPH, 0.01% of heavy metals and 0.05% of salt concentration [60]. This dilution effect shows that the volume of the top soil and the property of the land used for this purpose are the most critical (decision-making) factors because the volume of the drill cuttings can be controlled conveniently.
In general, reduction of the sodium concentration in the drilling waste and nutrient rich soil are precondition for optimal waste treatment. This is why calcium sulphate is usually applied to drilling wastes and fertilizers (both natural and synthetic) are applied to soil before or during treatment process [61]. It is important not to exploit the land excessively (regeneration time of not less than three years) to avoid damaging the soil, which can be hardly corrected. Recommended soil layer for land farming in the treatment of drill cutting is between 4-6 inches [1]. This treatment layer is called biocells. Pretreating the drill cuttings by composting and instigation of optimal conditions (like sufficient aeration and pH) through biopiling will reduce the acreage of waste meant for the land farming. Composting in this sense implies mixing the drill cuttings with sizable residual organic materials, which creates exothermic condition and stimulates microbial degradation of the hydrocarbons [62, 63]. Biopiling is a variant of land farming with the uniqueness of having systems that controls oxygen supply, moisture, temperature and pH. The pretreatment of drill cuttings by composting and biopiling will achieve ten times degradation rate of hydrocarbons in comparison to land farming alone. This shows that the amenability of land farming for drill cuttings treatment lies in its dual purposes: majorly for disposal, and elimination. Other drill cuttings disposal options, according to preference, are offshore discharge (after secondary treatments: thermal desorption and cutting dryer system), landfills and cutting re-injections [64, 27, 65].
Land farming is frequently used as a treatment option because it has high potential of success besides other advantages. Successes have been attributed to land farming in remediating oil-polluted soil, both intentional or accidental. The technique is suitable for easily or recalcitrant pollutants, is amenable for in situ and ex situ scenario but more adapted to aerobic condition [66]. Land farming was used record 80% removal of oil-contamination in 15 months in Kuwait [46, 51]. demonstrated that 90% of hydrocarbons were removed through the use of land farming technique apart from the fact that the soil fertility was modifies characterized with calcium and pH increase and P2O5 decrease. Yang et al. (2000) recorded 72.7% rate degradation of crude oil in a space of five months. [67] recorded a reduction of 80% of hydrocarbons in 11 months of land farming directed bioremediation. This was followed with increased enzymatic activities relative to a control soil. [68] demonstrated that application of land farming in treating drilling wastes does not pose threat of heavy metal increase nor their accumulation in plants in New Zealand agricultural system.
Pros and Cons of treating drill cuttings with land farming
Land farming allows for multiple waste loading on the same land, apart from its low-technology requirement, cost-friendliness and including its potential in positively modifying soil conditions [53]. Pre-treated drill cuttings is used in construction-related purposes including road construction, block manufacturing and as fill material [69, 70]. Though the overall technique is cheap, cost for its operation and maintenance (which involves periodic tilling and application of fertilizer, chemical analysis, and monitoring) is high considering also the possible cost of removing salt content from drill cuttings. The salt removal approaches include mechanical washing (using freshwater), leaching pads and calcium ion addition [64]. There is possibility of accumulation of recalcitrant pollutants and salts after extensive use of same parcel of land for treatment of drill cuttings.[71-75] This will ultimately do a damage to the land, making such land unsuitable for further waste treatment, setting in of soil-water repellency, [75-80] limited support for plant growth and microbial diversity [59].
Conclusion
The conclusion drawn from this mini review is as follows:
1. Drill cuttings is an hazardous waste of oil and gas exploration consisting of hydrocarbons, heavy metals and drilling fluids chemical additives 2. There are three basic sources of drill cuttings, which are oil-based muds, synthetic-based muds and water-based muds with decreasing toxicity effects 3. Drill cuttings managements include but not exclusive to waste minimization, secondary treatment and disposal 4. Drill cuttings causes physical, chemical and biological alteration of the ecosystem and its receptors be it microorganism, plants, animals and humans 5. Physicochemical treatment techniques are available for the management of drill cuttings but only the biological option guarantees sustainability 6. The many biological options available only land farming, composting and biopiling has been successfully used in field-scale 7. These three biological methods can be integrated in achieving 10 times of efficiency in comparison to the land farming method alone. 8. The land farming technique serves as both treatment and disposal options, making it the most popular amongst the biological alternatives available for drill cuttings treatment.
References
- Onwukwe SI, Nwakaudu MS (2012) Drilling wastes generation and management approach. Int J Environ Scie and Develop 3: 252.
- Saleh TA, Ibrahim MA (2019) Advances in functionalized Nanoparticles based drilling inhibitors for oil prodction. Energy Reports 5: 1293-304.
- Gaevaya EV, Tarasova SS, Zaharova EV (2019) Ways of Drilling Wastes Utilization Using Ecologically Safe Materials. In IOP Conference Series: Earth and Environ Sci 272: 032054. IOP Publishing.
- Micallef A, Person M, Berndt C, Bertoni C, Cohen D, et al. (2021) Offshore freshened groundwater in continental margins. Reviews of Geophysics 59: p.e2020RG000706.
- McFarland ML, Feagley SE, Provin TL (2009) Land application of drilling fluids: Landowner considerations. AgriLife Extension SCS 8: 1-5.
- Nguyen TT, Paulsen JE, Landfald B (2021) Seafloor deposition of water-based drill cuttings generates distinctive and lengthy sediment bacterial community changes. Marine Pollution Bulletin 164: 111987.
- Hu G, Liu H, Rana A, Li J, Bikass S, et al. (2021) Life cycle assessment of low-temperature thermal desorption-based technologies for drill cuttings treatment. J Hazardous Mater 401: 123865.
- Henry LA, Harries D, Kingston P, Roberts JM (2017) Historic scale and persistence of drill cuttings impacts on North Sea benthos. Marine environ res 129: 219-28.
- Baloyan BM, Chudnova TA, Anatolievich SD (2019) Environmental justification of the use of drill cuttings in the soil. Int Agric J.
- Ball AS, Stewart RJ, Schliephake K (2012) A review of the current options for the treatment and safe disposal of drill cuttings. Waste Manage & Res 30: 457-73.
- Veil JA, Dusseault MB (2003) Evaluation of slurry injection technology for management of drilling wastes (No. ANL/EA/RP-109792). Argonne National Lab., IL (US).
- Zhang X, Yao A (2019). Pilot experiment of oily cuttings thermal desorption and heating characteristics study. J of Petroleum Exploration and Production Technol 9: 1263-70.
- Mota AC, Santos JM, Pereira MS, Ataíde CH (2020) Microwave drying of olefins from drill cuttings and analysis of the organic phase recovered during drying operation. Oil & Gas Science and Technology–Revue d’IFP Energies nouvelles, 75: 1.
- Zhang H, Ma D, Qiu R, Tang Y, Du C (2017) Non-thermal plasma technology for organic contaminated soil remediation: A review. Chem Eng J 313: 157-70.
- Knox D, Jiang P (2005) Drilling further with water-based fluids-selecting the right lubricant. In SPE International Symposium on Oilfield Chemistry. Society of Petroleum Engineers.
- Fontana KB, Araujo RGO, de Oliveira FJ, Bascuñan VL, de Andrade Maranhão T (2021) Rare earth elements in drill cutting samples from off-shore oil and gas exploration activities in ultradeep waters. Chemosphere 263: 127984.
- Abbe OE, Grimes SM, Fowler GD, Boccaccini AR (2009) Novel sintered glass-ceramics from vitrified oil well drill cuttings. J Mater Sci 44: 4296-302.
- Stuckman MY, Lopano CL, Berry SM, Hakala JA (2019) Geochemical solid characterization of drill cuttings, core and drilling mud from Marcellus Shale Energy development. J Natural Gas Sci and Eng 68: 102922.
- Thomas G (2012) Diamond Core Drilling: Theory Mechanisms and Applications. Manchester, England, United-Kingdom.
- Adekunle IM, Igbuku AO, Oguns O, Shekwolo PD (2013) Emerging Trend in Natural Resource Utilization for Bioremediation of Oil—BasedDrillingWastesinNigeria. Biodegradation: Engineering and Technol 389.
- Tao S, Pan Z, Tang S, Chen S (2019) Current status and geological conditions for the applicability of CBM drilling technologies in China: A review. Int J Coal Geol 202: 95-108.
- Boutammine H, Salem Z, Khodja M (2020) Petroleum drill cuttings treatment using stabilization/solidification and biological process combination. Soil and Sediment Contamination: An Int J 29: 369-83.
- Hamed SB, Belhadri M (2009) Rheological properties of biopolymers drilling fluids. J Petroleum Sci and Eng 67: 84-90.
- Daneshfar MA, Ardjmand M (2021) A new approach in the optimal site selection of landfills for drilling cuttings from petroleum and gas fields. Chemosphere 270: 129402.
- Chen C, Li D, Sun N, Ma X, Xiao G, et al. (2021) Oil recovery from drilling cuttings by biosurfactant from kitchen waste oil. Energy Sources, Part A: Recovery, Utilization, and Environ Effects 43: 314-25.
- Liu H, Büscher JV, Köser K, Greinert J, Song H, et al. (2021) Automated activity estimation of the cold-water coral lophelia pertusa by multispectral imaging and computational pixel classification. J Atmospheric and Oceanic Technol 38: 141-54.
- IOGP. International Association of Oil & Gas Producers (2016) Environmental fates and effects of ocean discharge of drill cuttings and associated drilling fluids from offshore oil and gas operations. Report No. 543.
- Cochrane SKJ, Ekehaug S, Pettersen R, Refit EC, Hansen IM, et al. (2019) Detection of deposited drill cuttings on the sea floor - a comparison between underwater hyperspectral imagery and the human eye. Marine Pollution. Bulletine 145: 67–80.
- Paine MD, Skinner MA, Kilgour BW, DeBlois EM, Tracy E (2014) Repeated-measures regression designs and analysis for environmental effects monitoring programs. Deep Sea Research Part II: Topical Studies in Oceanography, 110: 84-91.
- Cui Z, Luan X, Li S, Zhao X, Lin Z, et al. (2020) Genotoxicity detection of oil-containing drill cuttings by Comet assay based on a demersal marine fish Mugilogobius chulae. Ecotoxicol and Environ Safety 208: P111655.
- Vora M, Sanni S, Flage R (2021). An environmental risk assessment framework for enhanced oil recovery solutions from offshore oil and gas industry. Environmental Impact Assessment Review 88: 106512.
- Knol-Kauffman M, Solås AM, Arbo P (2021) Government-industry dynamics in the development of offshore waste management in Norway: from prescriptive to risk-based regulation. J Environ Planning and Manage 64: 649-70.
- Rugatiri J (2021) Assessing Solid Waste Management Strategy in Higher Education Institutions of Indonesia: A Case Study of IPB University (Doctoral dissertation, IPB University).
- Sadiq R, Husain T, Veitch B, Bose N (2003) Evaluation of generic types of drilling fluid using a risk-based analytic hierarchy process. Environ manage 32: 778.
- Lyu S, Wang S, Chen X, Shah SM, Li R, et al. (2019) Experimental study of a degradable polymer drilling fluid system for coalbed methane well. J Petroleum Sci and Eng 178: 678-90.
- Guan Z, Chen T, Liao H (2021) Drilling Fluids. In Theory and Technology of Drilling Engineering 173-204. Springer, Singapore.
- Husveg T, Husveg R, van Teeffelen N, Verwey R, Guinee P (2021) Reviewing Cyclonic Low-Shear Choke and Control Valve Field Experiences. SPE Production & Operations 1-16.
- Hari S (2021) The 3R Concept and Waste Minimization. GDRC Reseaarch Output - Concept Note Series E-093. Kobe, Japan: Global Development Research Center. Retrieved from https://www.gdrc.org/uem/waste/3r-minimization.html [accessed Sunday, 14 March 2021]
- Sui D, Zhan M, Sui D, Zhao F (2021) Regulations and methods for disposal of waste drilling fluid. In IOP Conference Series: Earth and Environ Sci 631: 012045). IOP Publishing.
- Wang Z, Hao M (2021) Effects of Spent Drilling Fluids from Natural Gas Fields on Seed Germination and Root Development of Maize (Zea mays L.). Sustainability 13: 1510.
- Li Z, Zhou Y, Meng X, Wang S (2021) Harmless and efficient treatment of oily drilling cuttings. J Petroleum Sci and Eng 108542.
- Appleton TJ, Colder RI, Kingman SW, Lowndes IS, Read AG (2005) Microwave technology for energy-efficient processing of waste. Applied energy, 81: 85-113.
- Arpornpong N, Padungpol R, Khondee N, Tongcumpou C, Soonglerdsongpha S,et al. (2020) Formulation of bio-based washing agent and its application for removal of petroleum hydrocarbons from drill cuttings before bioremediation. Frontiers in Bioeng and Biotechnol 8: 961.
- Thapa B, Kumar KCA, Ghimire B (2012) A review on bioremediation of petroleum hydrocarbon contaminants in soil. J Sci Eng and Tech 8: 164-70.
- Rojas-Avelizapa N, Roldan-Carrillo T, Zegarra-Martinez H, Munoz-Colunga AM, Fernandez-Linares LC (2007). A field trial for an ex-situ bioremediation of a drilling mud-polluted site. Chemosphere 66: 1595-1600.
- Al-Awadhi R Al-Daher, A EINawawy, MT Salba (1996) Bioremediation of Oil-Contaminated Soil in Kuwait. I. Landfarming to Remediate Oil-Contaminated Soil. J Soil Contamination 5: 243-60.
- Ighilahriz K, Khodja M, Haddadi S, Benchouk A, Boutamine H (2021) Bioremediation of oily sludge contaminated site—a pilot-scale study. In Materials Res and Appl (pp. 241-250). Springer, Singapore.
- Whitaker AH (2014) Land Application of Drilling Mud from Oil and Gas Exploration: Agronomic and Environmental Implications (Doctoral dissertation, Oklahoma State University).
- Clements K, Veil JA, Leuterman AJ (2010) Global practices and regulations for land application and disposal of drill cuttings and fluids. In SPE International Conference on Health, Safety and Environment in Oil and Gas Exploration and Production. Society of Petroleum Engineers.
- Cansfield PE, Racz GJ (1978) Degradation of hydrocarbon sludges in the soil. Can J Soil Sci 58: 339-45.
- Chaineau CH, Morel JL, Oudot J (1996) Land treatment of oil‐based drill cuttings in an agricultural soil Am Society of Agronomy, Crop Sci Society of Am, and Soil Sci Society of Am 25: 858-67.
- Truu J, Truu M, Espenberg M, Nõlvak H, Juhanson J (2015) Phytoremediation and plant-assisted bioremediation in soil and treatment wetlands: a review. The Open Biotechnol J 9.
- Brown DM, Okoro S, van Gils J, van Spanning R, Bonte M, et al. (2017) Comparison of land farming amendments to improve bioremediation of petroleum hydrocarbons in Niger Delta soils. Sci of the Total Environ 596: 284-92.
- Hou D, O’Connor D, Igalavithana AD, Alessi DS, Luo J, et al. (2020) Metal contamination and bioremediation of agricultural soils for food safety and sustainability. Nature Reviews Earth & Environ 1: 366-81.
- Sayara T, Sarrà M, Sánchez A (2010) Optimization and enhancement of soil bioremediation by composting using the experimental design technique. Biodegradation 21: 345-56.
- Juwarkar AA, Singh SK, Mudhoo A (2010) A comprehensive overview of elements in bioremediation. Reviews in Environ Sci and biotechnol 9: 215-88.
- Kujawska J, Pawłowska M (2020) Effect of drill cuttings addition on physicochemical and chemical properties of soil and red clover (Trifolium pretense L.) growth. Plos one 15: e0242081.
- Hajabbasi MA (2016) Importance of soil physical characteristics for petroleum hydrocarbons phytoremediation: A review. Afr J Environ Sci and Tech 10: 394-405.
- Mkpaoro MIF, Okpokwasili GC, Joel OF (2015) A Review of Drill-Cuttings Treatment and Disposal Methods in Nigeria-The Gaps and Way Forward. In SPE Nigeria Annual International Conference and Exhibition. Society of Petroleum Engineers.
- Somee MR, Shavandi M, Dastgheib SMM, Amoozegar MA (2018). Bioremediation of oil-based drill cuttings by a halophilic consortium isolated from oil-contaminated saline soil. 3 Biotech 8: 1-13.
- Skipin L, Petukhova V, Gaevaya E, Zakharova E, Mitrikovskiy A (2016) Comparative effect of different coagulants on physical properties of drill cuttings. In Materials Science Forum 871: 33-241 Trans Tech Publications Ltd.
- Ayotamuno JM, Okparanma RN, Araka PP (2009) Bioaugmentation and composting of oil-field drill-cuttings containing polycyclic aromatic hydrocarbons (PAHs). J Food, Agric and Environ 7: 658-64.
- Alkoaik FN, Abdel-Ghany AM, Rashwan MA, Fulleros RB, Ibrahim MN (2018) Energy analysis of a rotary drum bioreactor for composting tomato plant residues. Energies 11: 449.
- Page PW, Greaves C, Lawson R, Hayes S, Boyle F (2003) Options for the recycling of drill cuttings. proceedings SPE/EPA/DOE Exploration and Production Environmental Conference, 10-12 March, San Antonio, Texas, U.S.A.
- de Almeida PC, Araújo ODQF, de Medeiros JL (2017) Managing offshore drill cuttings waste for improved sustainability. J cleaner production 165: 143-56.
- Soczo and Visscher (1987) Biological Treatment Techniques Contaminated Soil. (1987). Resources and Conservation 15: 125-136.
- Marin JA, Hernandez T, Garcia C (2005) Bioremediation of oil refinery sludge by landfarming in semiarid conditions: Influence on soil microbial activity. Environ res 98: 185-95.
- Okafor CM, Jeyakumar P, Anderson CW (2016) does land application of drilling waste pose a threat to new zealand agricultural systems?.
- Foroutan M, Hassan MM, Desrosiers N, Rupnow T (2018) Evaluation of the reuse and recycling of drill cuttings in concrete applications. Construction and Building Materials, 164: 400-9.
- Yetskalo V (2014) British Columbia's approach to drill cuttings disposal: is legislation fit for the purpose? Royal Roads University (Canada).
- Bevandić S, Blannin R, Vander Auwera J, Delmelle N, Caterina D, et al. (2021) Geochemical and mineralogical characterisation of historic Zn–Pb mine waste, Plombières, East Belgium. Minerals 11: 28.
- Djuric A (2012) Land-based disposal rules and regulations: how three different high-performance fluids rate in three different regions. In International Conference on Health, Safety and Environment in Oil and Gas Exploration and Production. Society of Petroleum Engineers.
- Ghasemi, S., Gitipour, S., Ghazban, F., & Hedayati, H. (2017). Treatment of petroleum drill cuttings using stabilization/solidification method by cement and modified clay mixes. Iran J Health, Safety and Environ 4: 781-7.
- Huang Z, Xu Z, Quan Y, Jia H, Li J, et al. (2018) A review of treatment methods for oil-based drill cuttings. In IOP Conference Series: Earth and Environ Sci 170: 022074.
- Ismail AR, Alias AH, Sulaiman WRW, Jaafar MZ, Ismail I (2017) Drilling fluid waste management in drilling for oil and gas wells. Chemical Engineering Transactions, 56: 1351-6.
- Jiang G, Yu J, Jiang H, Xu B, Tang P, et al. (2020) Physicochemical characteristics of oil-based cuttings from pretreatment in shale gas well sites. J Environ Sci and Health, Part A 55: 1041-9.
- Nemerow LN (2007) Industrial Waste Treatment, Boston
- Pereira MS, de Ávila Panisset, CM, Martins AL, de Sá CHM, de Souza Barrozo MA, Ataíde CH (2014). Microwave treatment of drilled cuttings contaminated by synthetic drilling fluid. Separation and Purification Technology, 124, 68-73.
- Veil JA (2002) Drilling waste management: past, present, and future. In SPE Annual Technical Conference and Exhibition.
Artcle Information
Review Article
Received Date: September 13, 2021
Accepted Date: October 13, 2021
Published Date: October 14, 2021
World Journal of Environmental Science and Energy
Volume 1 | Issue 1
Citation
Emmanuel Oliver Fenibo (2021) Suitable Train of Bioremediation Techniques for Secondary Treatment of Drill Cuttings. Environ Sci Energy 1(1):108
©2021 Emmanuel Oliver Fenibo. This is an open-access article distributed under the terms of the Creative Commons Attribution License, which permits unrestricted use, distribution, and reproduction in any medium, provided the original author and source are credited.
doi: jese.2021.1.108